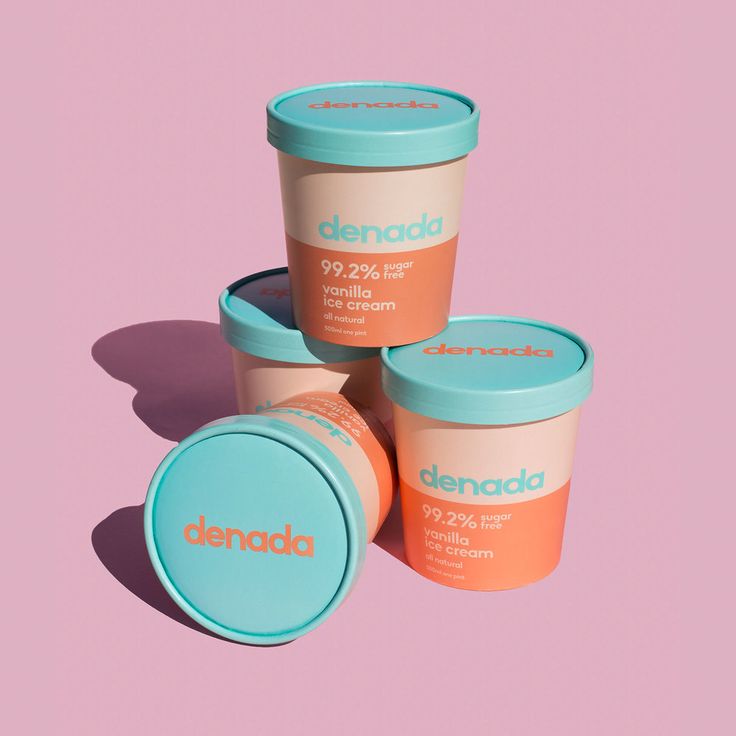
Introduction
What are IML Containers? A Comprehensive Guide and Their Applications in Packaging
IML Containers: Guide & Applications in Packaging; it is the first point of contact a customer has with your brand. IML (In-Mold Labeling) containers, as one of the advanced technologies in packaging, have brought significant changes in the design, attractiveness, and durability of plastic containers. With the increasing need for durable and environmentally friendly packaging, IML has quickly established itself as an innovative, cost-effective, and recyclable solution in the food, health, and many other industries. In this article, we will examine the IML technology, various production methods, and its benefits in detail to gain a complete understanding of this novel method.
What are IML Containers?
IML Containers: Guide & Applications in Packaging
What are IML Containers? A Comprehensive Guide and Their Applications in Packaging
IML Containers (In-Mold Labeling) are containers where labels are directly placed inside the mold during the manufacturing process and become integrated with the molten plastic as it forms. This technology ensures that the label is permanently and securely attached to the container, providing a beautiful and professional design, while also maintaining high technical quality. These labels are resistant to abrasion, moisture, heat, and chemicals. This method is widely used in various industries such as food, healthcare, detergents, and cosmetics to produce durable and attractive containers.
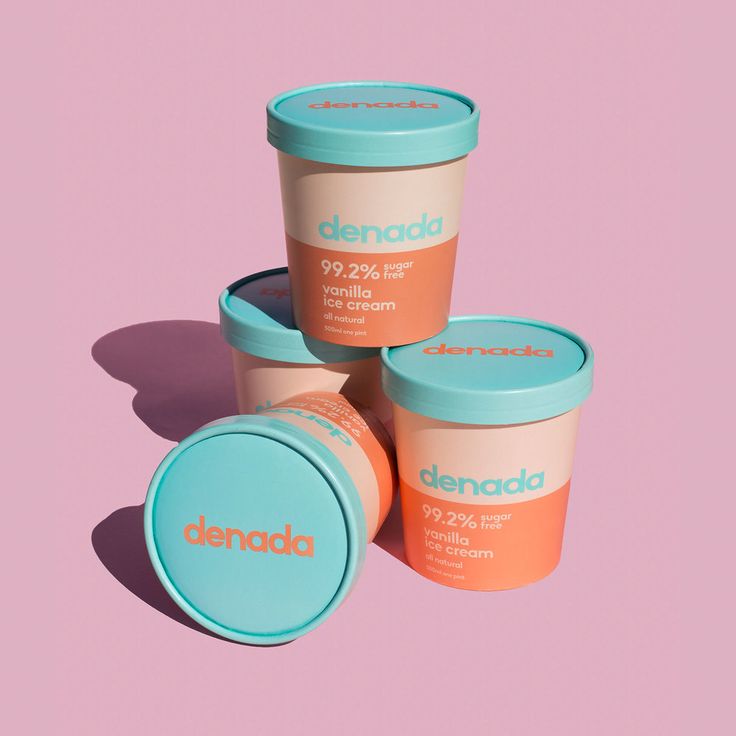
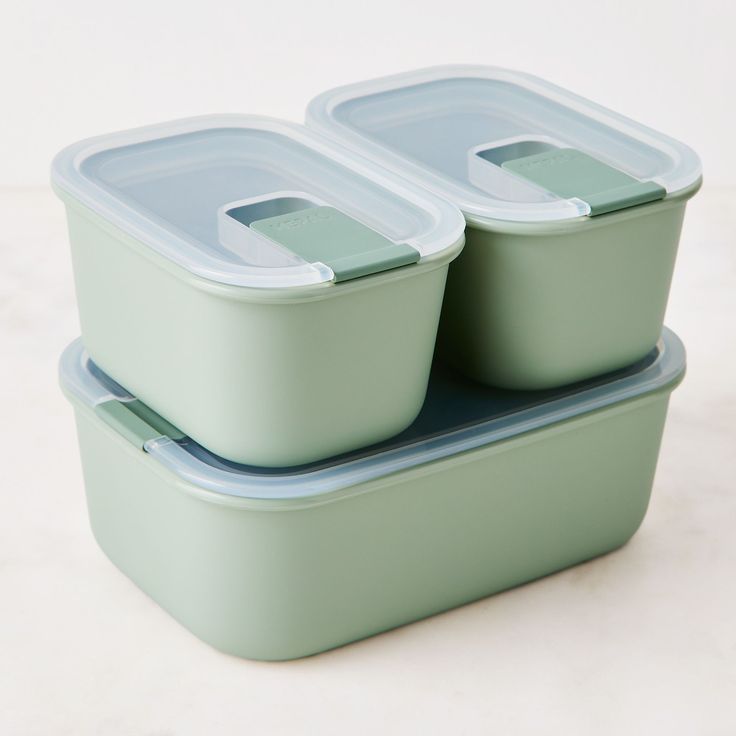
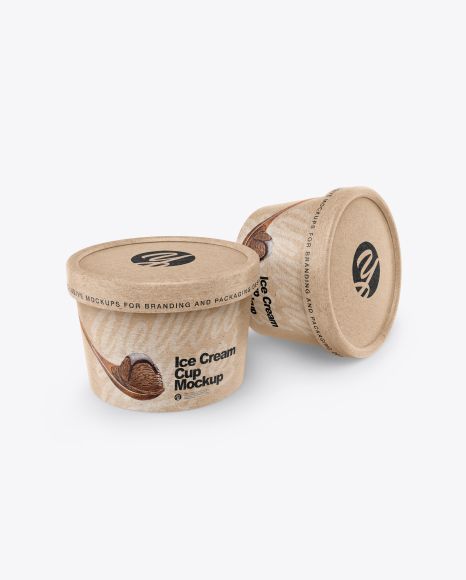
IML Container Production Methods
- Injection Molding: In this method, the IML label is placed in its designated position before the plastic material is injected into the mold. The molten plastic is then poured into the mold, and after cooling, the final container with the integrated and durable label is formed. This method, which is used in over 68% of IML container production, is ideal for producing containers with various shapes and thin walls.
- Blow Molding: The blow molding method is used to produce hollow containers such as bottles and larger containers. The label is placed inside the mold, and then molten plastic is blown into the mold. In this process, the label merges with the plastic and adheres to the outer surface of the container. This method accounts for approximately 31% of IML container production.
- Thermoforming (Thermoforming – TIML): The thermoforming method is used for producing containers that require thicker and more durable walls. In this method, a plastic sheet is heated and then compressed with a mold to shape the container. With only 1% application, this method is suitable for producing more durable and specialized containers.
IML Containers produced by Jilafe Plast are manufactured using the best injection molding technology and offset printing. Click to view samples.
Advantages of IML Containers
- Attractive and Visual Design
- IML labels allow designers to print high-quality images and a variety of colors on containers. These labels can include logos, product information, and creative designs that enhance the attractiveness of the packaging.
- High Durability and Longevity
- IML labels are made from durable materials that are resistant to abrasion, water, and chemicals. As a result, both the label and the container maintain their quality over time, presenting a clean and unified appearance.
- Environmentally Friendly
- One of the most important advantages of IML containers is their recyclability. Since the label and the container are made from similar materials, they can be easily recycled after use, which helps in reducing plastic waste.
- Temperature Resistance and Storage Durability
- IML containers are capable of withstanding various temperatures. This feature makes IML containers suitable for packaging food items that need to be refrigerated as well as for storing detergents.
- Time and Cost Savings in Production
- The IML process, due to the integration of container production and labeling, does not require additional steps or labor. This reduces production time and saves costs.
For more information and to order IML containers, please contact us.
IML or Traditional Methods?
In traditional methods, labels are applied to the container after its production. This method is not only time-consuming, but the labels may also peel off when exposed to water or environmental factors. On the other hand, IML, due to the complete integration of the label and container, provides a high-quality appearance that is resistant to environmental conditions.
Applications of IML Containers in Various Industries
IML technology is used in various industries, including the following:
- Food Industry
- IML is used for yogurt, dessert, ice cream, and other food product containers due to its excellent resistance to cold and moisture.
- Healthcare and Detergent Industries
- IML is ideal for packaging detergent and healthcare products that require containers resistant to chemicals.
- Cosmetics
- IML is widely used in the packaging of cosmetics and personal care products where the beauty and durability of the packaging are important.
Summary: Why IML Containers Are a Superior Choice
IML plastic containers are an ideal choice for large and small companies due to their high durability, attractive design, environmental compatibility, and cost-effectiveness. Using IML allows companies to attract customer attention with creative and professional packaging while supporting the environment. This technology, with its high speed, lower costs, and greater efficiency, is the best option for companies seeking to offer high-quality products with a flawless appearance.
Frequently Asked Questions about IML Containers
Are IML containers heat-resistant?
Yes, IML containers are resistant to various temperatures due to the high durability of the materials used, and they can even be stored in refrigerated environments.
Is using IML cost-effective for all products?
IML, compared to traditional methods, incurs higher costs due to the need for specialized equipment and a higher minimum order quantity. However, it is more cost-effective for mass production.
Advanced Labeling IML Containers IML Technology Packaging Industry